Our Quality Policy
DICA Electronics Ltd is committed to ensuring customer satisfaction in product quality, delivery and customer service.
Our Primary Goal at DICA Electronics Ltd. is to manufacture and supply defect free products to our customers, on time, every time.
DICA Electronics Ltd. will continue to meet or exceed our customer’s expectations through effective quality planning and continual improvement efforts throughout the organization, which are driven by our quality objectives and our quality management system.
DICA Electronics Ltd. performs thorough inspections at the key points in the assembly process. We believe that cost efficiency and quality products are developed by building the assemblies correct the first time. We have built a strong reputation of high quality standards that is largely based on our detailed processes and our skilled employees.
Electrostatic Discharge (ESD) protection is implemented throughout the entire manufacturing floor. This includes the use of anti-static mats, anti-static workstations, smocks, wrist and heel straps, an ESD protective floor finish, and mechanical racking with full ESD protection.
Our manufacturing process from start to finish includes quality checks and inspections:
- Receiving: All incoming parts purchased for turnkey clients are inspected prior to being placed in inventory.
- Kit Verification: All consignment and turnkey builds are kitted based on the BOM supplied by our clients. We compare each part for the correct quantities and part IDs. If shortages are identified, a report is issued to the client and direction is documented.
- AOI Inspection – Post Print – The printed PCB is checked for solder paste deposition and issues such as bridging, insufficient solder, excess solder, solder volume, solder smearing and debris are identified.
- AOI Inspection – Post Reflow – The reflowed PCB’s are checked for problems such as component presence/absence, pad position, skew, polarity and damage.
- Final Inspection: All assemblies are inspected against the assembly drawing and manufacturing instructions provided for the assembly.
- Shipping: All shipments are inspected by a qualified final inspector to ensure all procedures have been done according to the paperwork for the assembly.
At DICA Electronics Ltd, we supply completed assemblies that meet or exceed our clients specified quality requirements and expectations. We strive to provide 100% customer satisfaction. We realize that to stay competitive, quality and efficiency are key.
Feedback:
Your satisfaction is important to us. We welcome all types of feedback. Please email us at feedback@dica.ca
DICA’s Quality Management System is AS9100 and ISO9001:2015 Certified.
DICA builds and inspects circuit boards to the IPC 610 Standard.
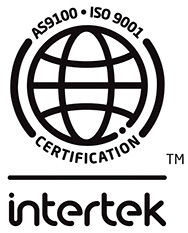